Recent News
Plasma Ignition and Emissions Devices Deliver Impressive Performance
June 18, 2020TPS Featured in Forbes – Plasma Ignition Sparks Higher Fuel Economy And Cleaner Emissions
February 1, 2020TPS Launches the Transient Plasma Surface Treatment System, Delivering Major Benefits Through Nanosecond Pulsed-Power Plasma
October 23, 2019TPS Qualifies as BusinessGreen Technology Awards 2019 Finalist
October 10, 2019Emissions Remediation Solution
Superior Emissions Remediation
for Clean Air Imperatives
Transient Plasma Emissions Remediation Systems offer revolutionary new tools to support clean air initiatives. TPS application-specific design configurations allow for seamless integration with a comprehensive range of diesel engine applications and commercial kitchen ventilation systems.
These innovative systems drastically reduce particulates and NOx in diesel emissions and significantly remediate harmful particulates, while also eliminating smoke and odor from commercial kitchens.
These innovative systems drastically reduce particulates and NOx in diesel emissions and significantly remediate harmful particulates, while also eliminating smoke and odor from commercial kitchens.
Diesel Engine
Applications
Typical Integration of the TPS Emissions Remediation Reactor and Power Supply with a Diesel Engine
The reactor configuration shown here is flexible depending on packaging constraints (i.e. different aspect ratios of length to diameter and number of electrodes are possible to enable effective particle remediation) while still accommodating volume constraints.
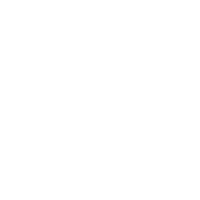
VS DPF
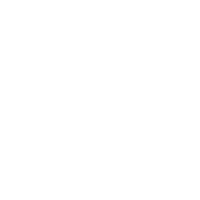
Easy to Inspect and Maintain
VS DPF
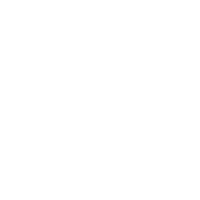
Low Power Consumption is <300 W (<1.6% Engine Power)
VS DPF
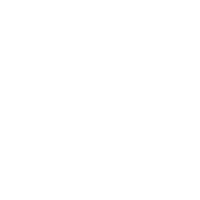
Reliable TPS Pulse Generator Tested Under Harsh Conditions
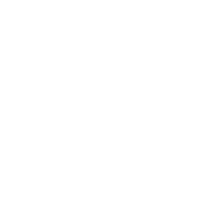
Scalable with Engine HP
Diesel Engine Test Results
TPS Emissions Remediation system was tested on a 18kW, 1800 RPM, 2.2 L diesel engine that meets Tier 4 emissions regulations, without any emissions control device (no DOC or DPF) at an independent test facility. The tests were conducted in accordance with modified (i.e. a 6-mode as opposed to a 4 mode) EPA test methodology 40 CFR 1065.601(c)(1) and 40 CFR 1039.645.
G2 Weighted 6-Mode Test
TPS OFF (g/BHP-hr)
0.0
TPS ON (g/BHP-hr)
0.00
REMEDIATION*
0%
*NOTE: Remediation was obtained with only 1.6% of engine power. With further optimization and incremental increase in engine power use, remediation can be extended beyond 85%.
Street Sweeper Exhaust NOx Reduction
NOx EMISSIONS REDUCTION
>0%
WITH PLASMA
At 0% Load and 1.5% Engine Power Used by TPS System
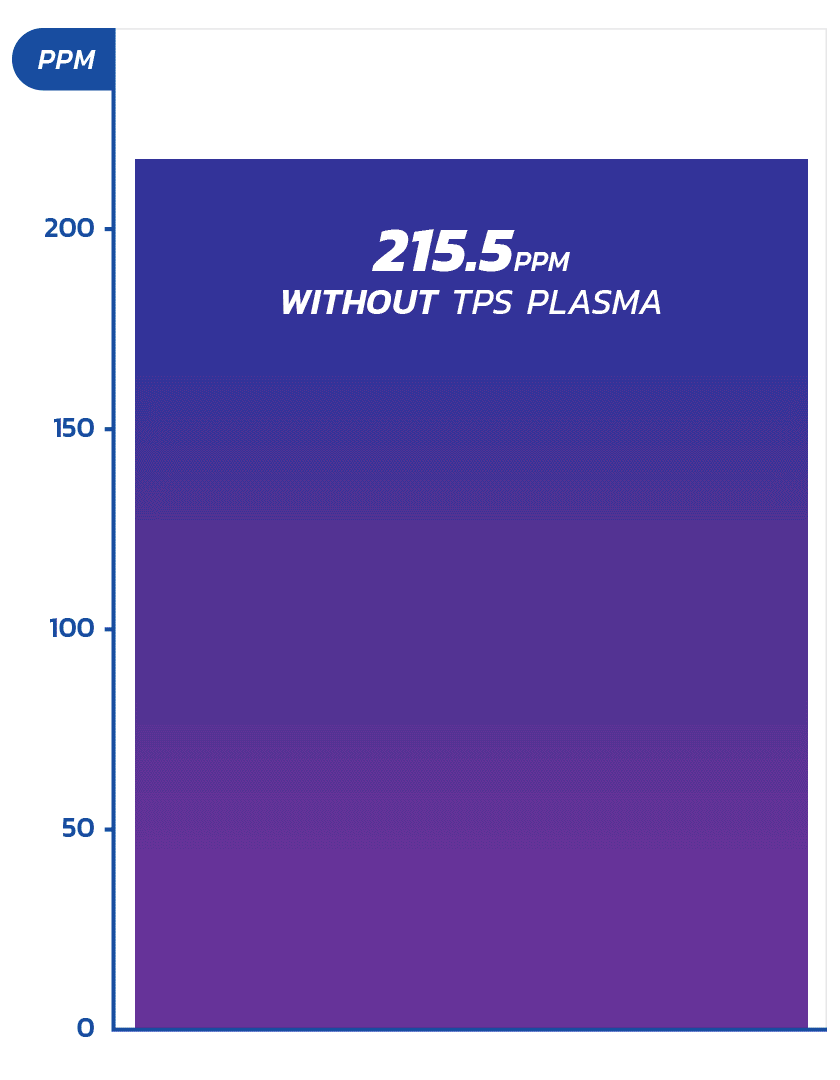
Commercial Kitchen
Applications
The Big Challenge
Research carried out by Universities and Environmental
Protection Agencies has found that commercial chargrills
produce greater amounts of air pollution than diesel trucks.
Studies claim that the amount of particulate matter (PM) that
these cooking systems send into the ecosystem is far more than
trucks and factory smokestacks.
Kitchen Ventilation Particulate
Emissions Reduction
Why Inhaling Burgers is Unhealthy
When grease drips onto a flame, it forms soot, which is composed of very fine particles that can work their way deep into the lungs. A high-fat hamburger cooked on a flame charbroiler emits significantly high amounts of PM. Research has found that every 1,000 pounds of hamburger cooked on conveyor broilers creates 25 pounds of emissions.
When grease drips onto a flame, it forms soot, which is composed of very fine particles that can work their way deep into the lungs. A high-fat hamburger cooked on a flame charbroiler emits significantly high amounts of PM. Research has found that every 1,000 pounds of hamburger cooked on conveyor broilers creates 25 pounds of emissions.
A Growing Appetite for Cleaner Air
Pressure continues to mount for heightened regulatory policy to curb harmful emissions. An increase in mixed-use building construction is also driving peer pressure to lower particulate, smoke and odor emissions from neighboring commercial kitchens.
While some solutions to post-treat the exhaust from industrial grills have emerged, they are costly and difficult to implement and maintain. Transient Plasma Systems emissions solutions hold the promise of exceptional PM mitigation performance, deep smoke and odor removal, and low maintenance. And that’s a breath of fresh air for commercial grill operators.
Pressure continues to mount for heightened regulatory policy to curb harmful emissions. An increase in mixed-use building construction is also driving peer pressure to lower particulate, smoke and odor emissions from neighboring commercial kitchens.
While some solutions to post-treat the exhaust from industrial grills have emerged, they are costly and difficult to implement and maintain. Transient Plasma Systems emissions solutions hold the promise of exceptional PM mitigation performance, deep smoke and odor removal, and low maintenance. And that’s a breath of fresh air for commercial grill operators.
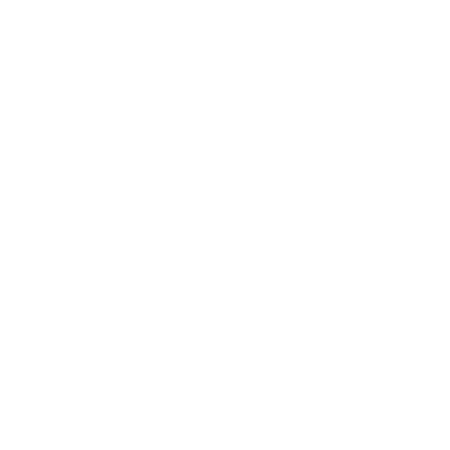
Plasma Technology Eliminates Particulates, Smoke, and Odor
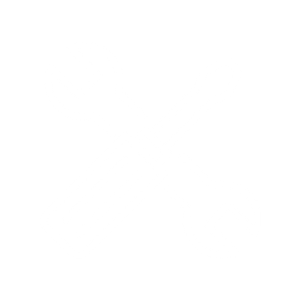
Simple System with Low Maintenance

Easy Integration with Kitchen Ventilation Systems
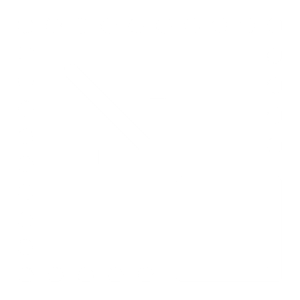
Minimizes Footprint and Eliminates Expensive Ductwork
Commercial Kitchen Ventilation Test
TPS Emissions Remediation system was tested on a commercial grade charbroiler at a test facility. Testing was conducted at 2000 CFM and 3000 CFM. Particle Remediation was measured using a Dekati-ELPI particle counter. Subjective measurements were used for visual smoke and odor remediation.
Commercial Kitchen Hamburger Emissions Remediation
AVERAGE TPS REMEDIATION
0%
20 BURGERS
TPS POWER USE: 805W
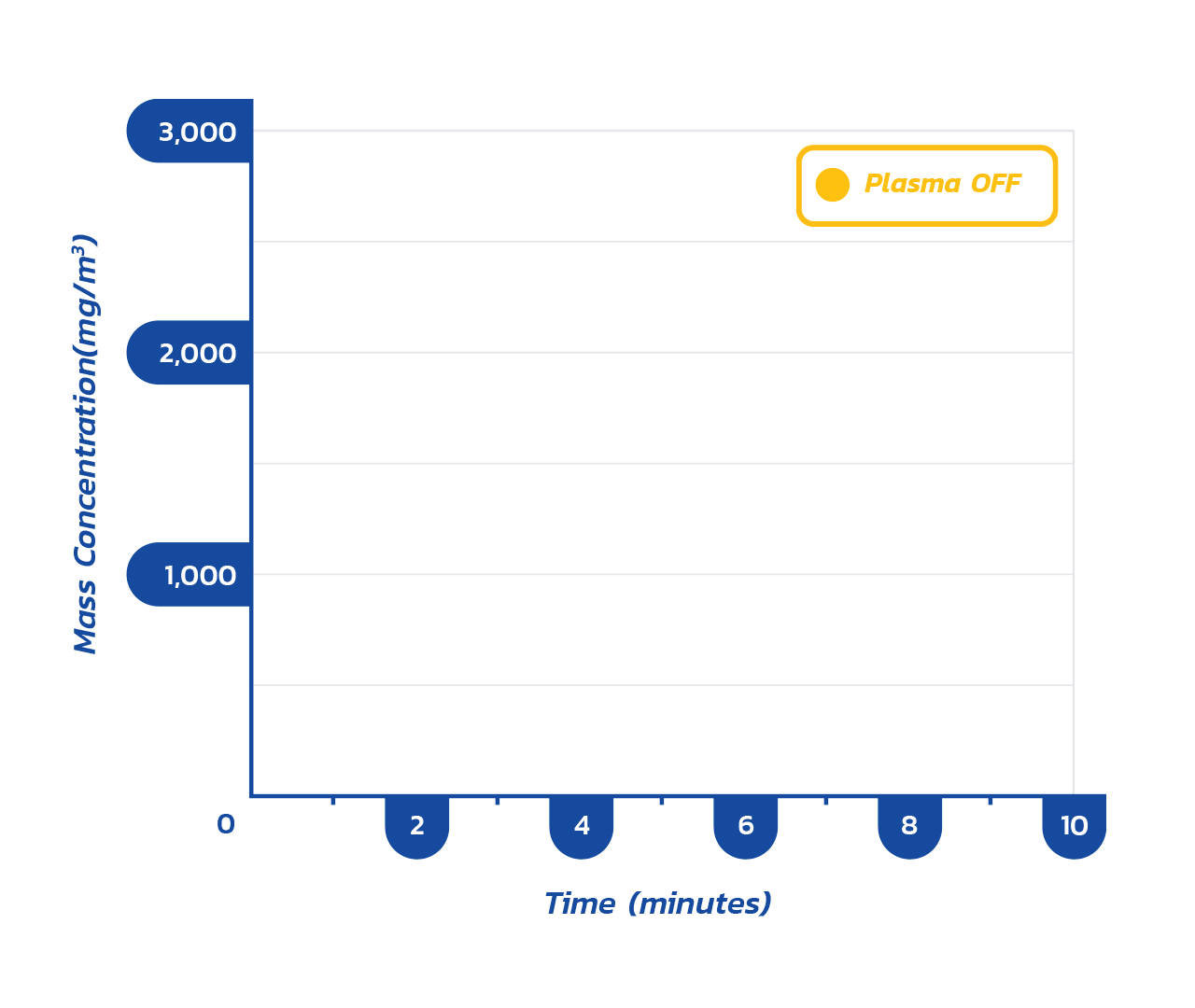
AVERAGE TPS REMEDIATION
0%
14 BURGERS
TPS POWER USE: 805W
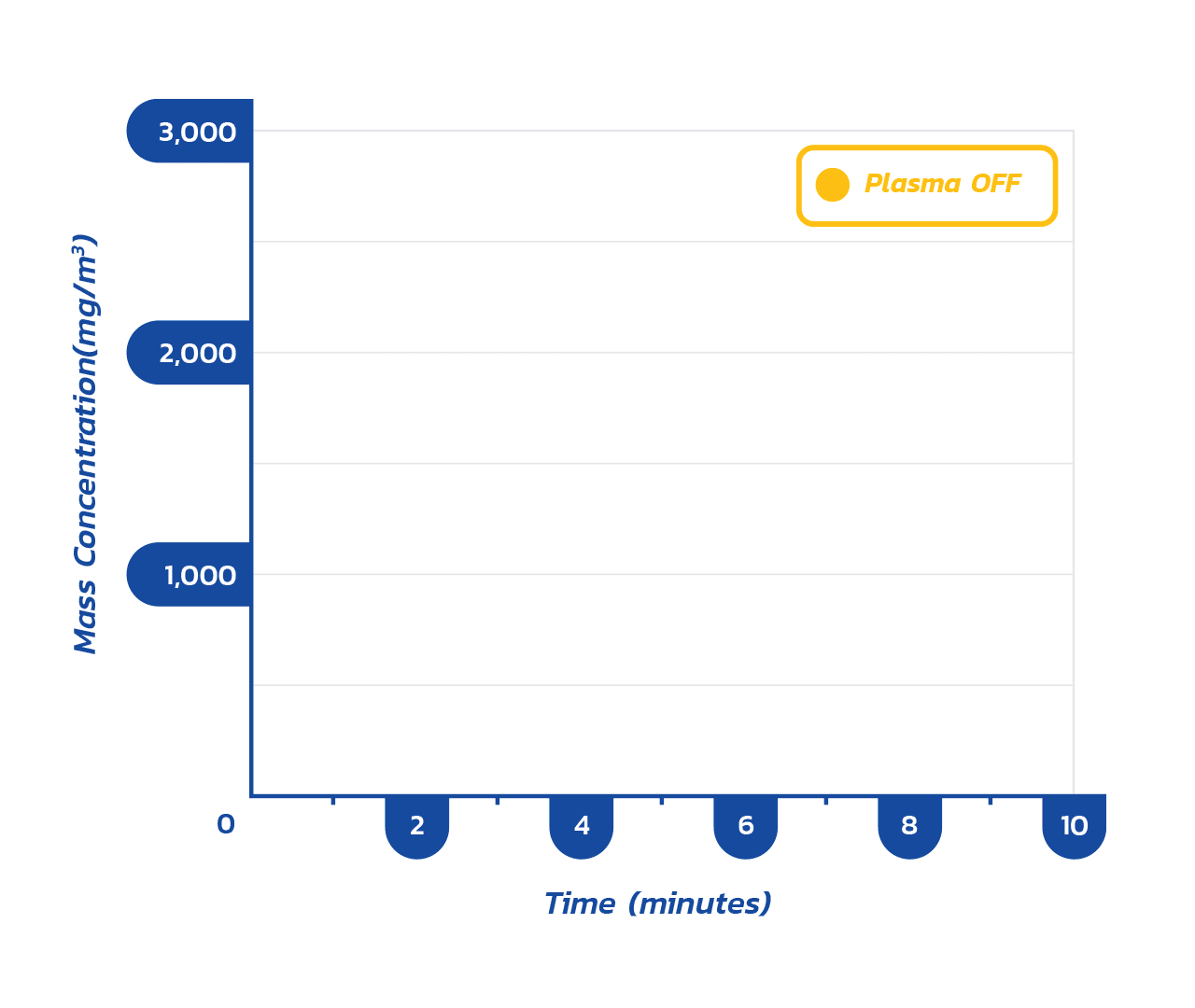
The TPS Difference
250x
More Efficient Than Other Plasma-Production Methods
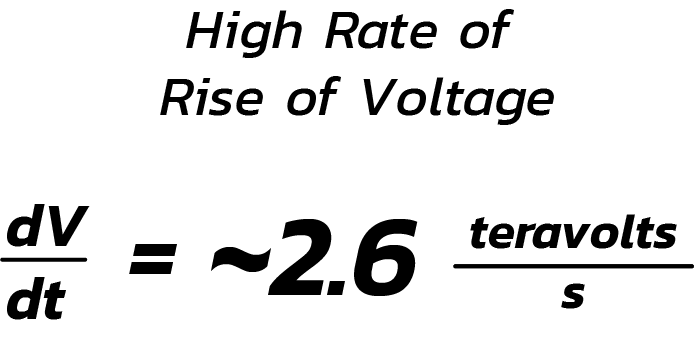
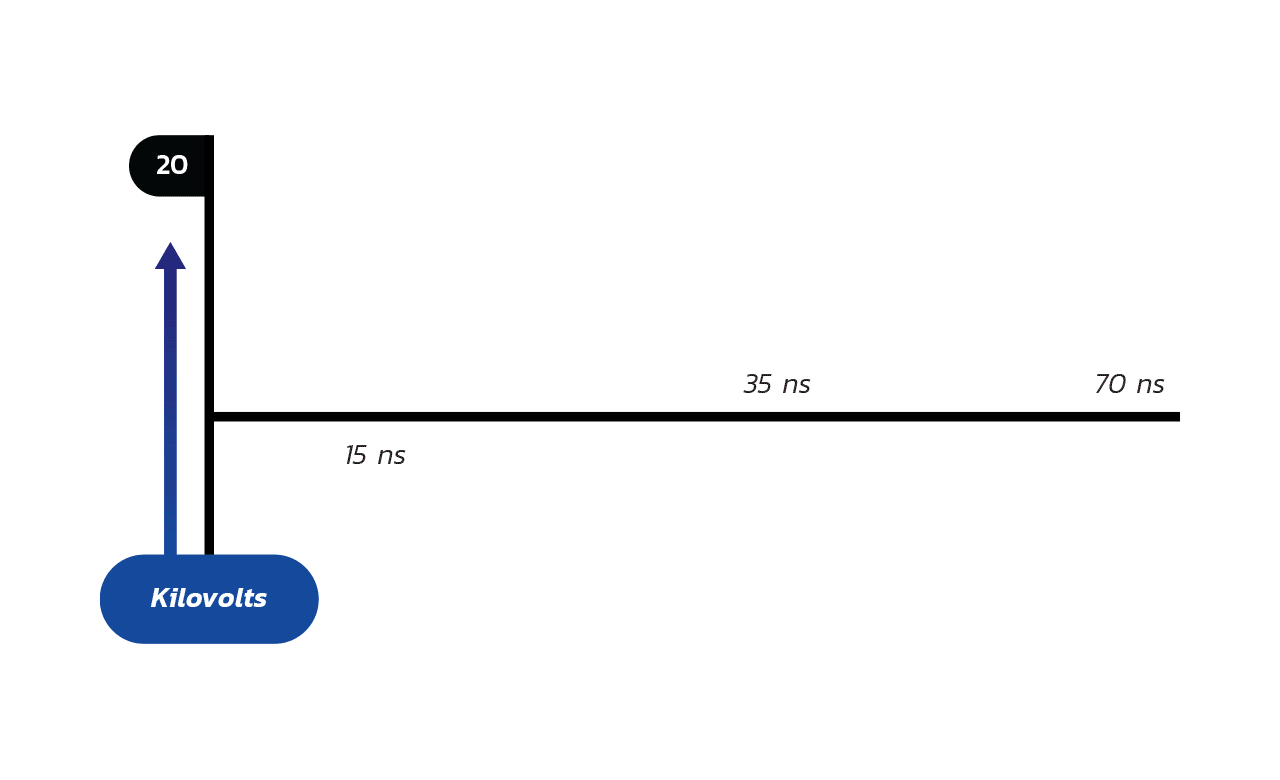
Transient Plasma Treatment of Diesel Exhaust Science
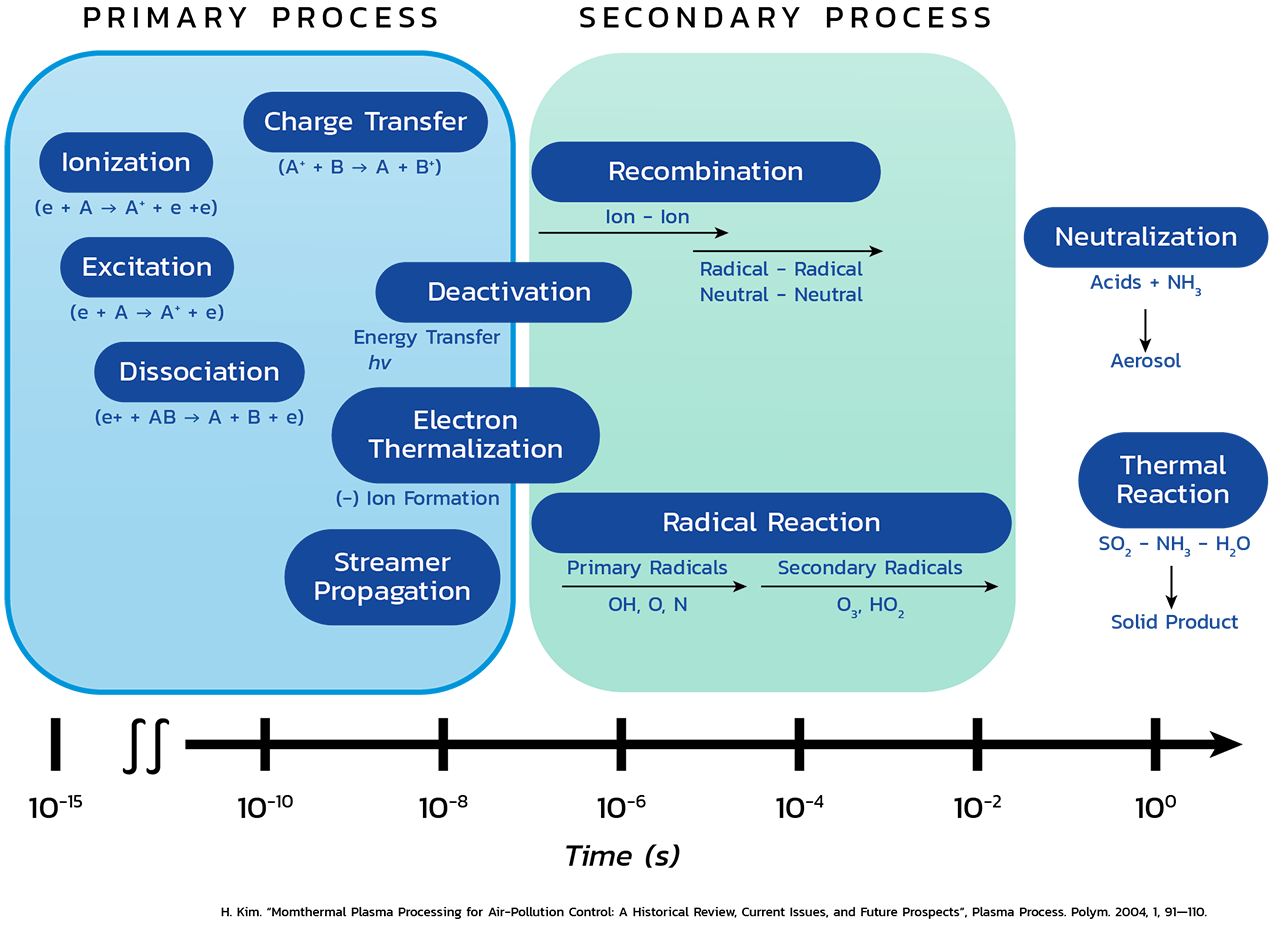